Excursion at DSM
The SGIG study group met at DSM in Sisseln at the end of last year. The company attributes the low accident rate of the Aargau-based chemical group to a differentiated "bottom-up" feedback culture. However, where very large numbers of chemical substances are worked with, occupational hygienists and complex hazardous substance analyses are also required.
Vitamins, pharmaceuticals and substances for the cosmetics industry and the food industry are manufactured at the DSM plant in Sisseln. Vitamin A is the group's largest product, of which more than 20,000 tons are produced annually in 100 different qualities. More than 1000 employees work at the Sisseln site, 100 of them in development. The fact that everything throughout the chain is produced and formulated in Sisseln is considered a special feature of the Aargau production facility.
Only a very small number of accidents per year are recorded, said plant manager René Vroege at the Erfa autumn conference of the SGIG study group in Sisseln. However, a milestone has not yet been reached. DSM also invests around CHF 20 million a year in the Health and Safety Environment area. An ASGS officer must ensure that all employees can work in peace and efficiently, says Kaja Düsterloh, Head of SHE Compliance.
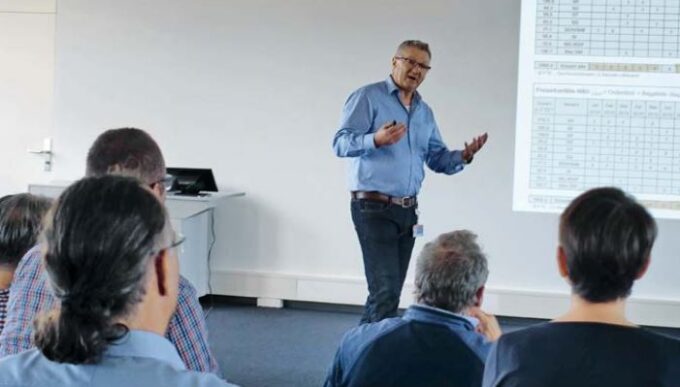
He says it is very important never to condemn employees when they make mistakes. The principle of basic trust applies: "Everyone wants to do a good job during the day, but no one is 100 percent focused throughout the day. Analyzing the course of an accident often reveals amazing things, he says. In most cases, accidents occur at the moment when a work process is deliberately approached differently. Inattention, for example after an unsuccessful or hectic day, is also a frequent cause of accidents. Thus, DSM focuses strongly on prevention and on the analysis of so-called near misses. The exchange takes place across the hierarchies. A great deal of attention is paid to employee feedback. For example, the introduction of new safety glasses, including vision correction, resulted in many near misses. According to Düsterloh, a feedback culture of this kind is also essential for employee communication in order to sound out potential for improvement at any time, because people tend to get tired and overestimate themselves, especially on hectic days.
Employees as ambassadors for non-occupational accidents
With regard to the recording of all accident incidents, various statistics are kept at DSM. The ratio between accidents and minor accidents has remained more or less identical in recent years. Last year, too, a top result was achieved with regard to occupational accidents, says Markus Hurst, expert for occupational safety at DSM. To achieve this, the company relies on various awareness campaigns, accompanied by various Suva modules such as the prevention program "Crime scene stairs" or practical transfers of learning units such as sun protection and smoke protection training. One favored approach is an internal training program called "SafeStart" - according to the motto "What you have learned at work, you should also apply at home if possible.
Internal short videos of employees attract special attention. For example, in short sequences of around two minutes, voluntary employees tell of a personal near-accident experience such as tripping accidents with a lawn mower. Afterwards, the video ambassadors themselves reflect on the possible consequences and causes of an accident in order to sensitize their work colleagues to the issue.
Purpose: Early recognition of one's own change in behavior in the event of personal experiences among employees can also improve prevention in the event of non-occupational accidents. For example, if an employee does not hold onto the handrail when using stairs, there is a high probability that he or she will be seriously injured in the event of a fall. Essentially, the idea is that early recognition of one's own emotional state, such as hecticness, fatigue, frustration and overestimation of one's own capabilities, should help prevent one from getting into a critical situation oneself. The decisive factor in all prevention work is therefore the change in behavior of everyone themselves, he said. "Only if accident risks are recognized and reflected upon at an early stage can accidents be prevented in good time," says the labor expert.
All substances can be toxic, the decisive factor is the dose
However, chemical exposure to certain substances can influence life expectancy as well as factors including hypersensitivity, allergies and cancer risk in the workplace. Occupational hygiene expert Ludovic Vieille-Petit from DSM spoke, among other things, about his task of quantifying exposure to substances hazardous to health in the workplace and how systematic protective measures are perceived in a chemical company.
"Even a substance that is non-toxic at low doses can be toxic at high doses," Vieille-Petit says. In addition to the qualitative consideration of the health-critical analysis, the occupational hygiene risk analysis includes the quantitative measurement of exposure to chemical substances at the workplace as well as the scientific consideration of toxicity in figures. Relevant factors include the duration of exposure and the exposure level of the measured exposures. A risk analysis, for example, cannot be done without determining exposure in order to define the appropriate measures, Vieille-Petit said. The DSM, for example, keeps an inventory of all products and their properties. By law, there is a "universal requirement" or obligation for employers to identify and control health risks, DSM says. Employers must know the hazards and exposures for which technical protection measures (also called "collective protection measures") must have a high priority.
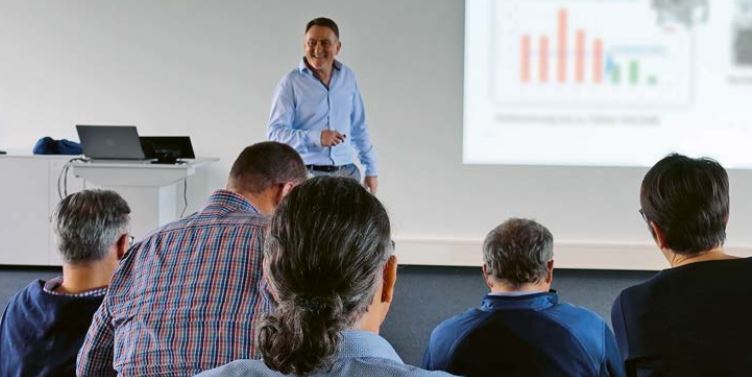
The actual uptake of substances generally occurs through the mouth, lungs, blood and/or skin. In the working environment, the respiratory tract and the skin are the most relevant routes of exposure. Crucial to DSM's measurements are air analyses by sampling and the corresponding investigations in the laboratory. When analyzing air samples, he said, it is essential to ensure that it is based on a validated measurement method. During method development, both sampling and analytical determination must be tested. In each case, the analysis must be substance-specific in order to be able to assign the substance below a certain level, Vieille-Petit says. A special exposure matrix knows 1-4 classification levels and is divided according to different exposure levels and time loads.
The exposure measurements in the air are carried out by trained occupational hygienists or trained specialists. The substance-specific exposure limit value (also called workplace limit value) is decisive for the interpretation of the measurement results. For example, 80 percent of the employee's vitamin A comes from their diet. For this reason alone, an employee may be exposed to a maximum of 20 percent of the recommended daily dose of vitamin A. The procedure for quantitative exposure determination consists of adsorption or desorption of the substance or of the sampling medium and subsequent analysis. It is also important to pay attention to how long a sample is "stable". The decisive factors are the smallest quantifiable quantities and the minimum evaluable risk limits. As a rule, for a given sampling period, it must be ensured that at least 10 percent of the exposure limit value can be quantified with sufficient reliability. However, there are also special features. When interpreting the measurement results, one thing is certain: at the end of an eight-hour shift, the workplace limit value must not be exceeded on average. There are also short-term exposure limit values of more than 15 minutes for certain chemical substances. The results of the air measurements are generally given as an average value over the effective duration of the activity or sampling. As a rule, the results are not converted to an eight-hour average value. Reason for that is,
However, there are always deviations from international standards and recognized best practices, explains the industrial hygienist. If a workplace limit value is not complied with under the existing conditions, employees must also be protected with personal protective equipment (PPE). However, PPE should be provisional or supplementary as far as possible. The aim is to keep exposure below an acceptable level using technical protective measures (also known as containment solutions).