Maintain gas detection systems
In an industrial plant, but also in production facilities, hazardous substances are part of everyday life. Reliable detection, but also a certain basic principle in the installation and maintenance of gas detection systems are therefore essential.
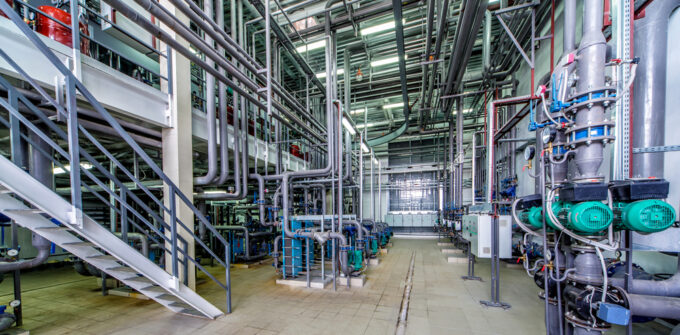
The challenges for an installer of gas detection systems in practice are manifold and not always easy to master, even with a lot of experience. The constant technical progress brings also always new challenges and makes thus a constant further training of the installers, companies, technical planners and safety representatives necessary.
As the industry evolves, so does our understanding of how to achieve a safe working environment for people. Nevertheless, there are various points that will remain the same in the future. When planning a gas detection system, the first question is always: Why do I need to detect these gases? This question is essential.
The second question that arises:
Is it explosion protection or personal protection? Or perhaps a combination of both - which is becoming increasingly common in practice. If these basic questions are properly analyzed and worked out, a solid basis is created on which to build. Further, it must be clarified how the gas behaves: is it heavier or lighter than air? Does it tend to outgas? How does it behave in terms of temperature and humidity? This is a very important question, because it has a direct influence on the choice of sensor.
Other criteria to consider from the planner's perspective:
- Do the gas detectors have to be installed in an Ex zone?
- Are gas drop controls present? What is meant by a gas drop control: for example, ventilations/switch-ons, closing gas valves, de-energizing circuits or a production process stop, etc.?
I would like to explain this in more detail using a practical example. Let's assume that a new refrigeration plant is installed at customer X, which is operated with NH3 (ammonia). The machine room of this plant is now to be monitored with a gas warning system (GWA).
In this specific case, Suva's leaflet "Operating refrigeration systems and heat pumps safely" an. Since NH3 corresponds to a refrigerant of safety class B2, the following requirements apply to the GWA according to Suva.
If the refrigeration system does not fall within the area of a permanently manned workplace, the alarm thresholds are set to the following values in practice according to Suva; otherwise the MAK value applies: The pre-alarm threshold is 10 percent LEL and a visual and audible alarm must be triggered on site. The main alarm threshold is max. 20 percent LEL. When this threshold is reached, the following additional measures must be taken: The entire plant and the machine room must be de-energized, except for the operating equipment with Ex zone conformity.
In practice, however, the following values with their associated measures have become established:
- at 50 ppm: ventilation ON
- at 200 ppm personal alarm ON
- at 900 ppm machine OFF
- at 30 000 ppm (20 percent LEL) load shedding and ventilation OFF.
Furthermore, when the main alarm is reached, there is a need to forward it to the responsible office.
If the machine room is additionally equipped with fire detectors, prioritization of the alarms must be defined. What is meant by this? With regard to ventilation, the following can be said: In the event of a fire, one does not want to carry the resulting smoke gases via the ventilation ducts into fire compartments without fire protection insulation.
In the case of an ammonia leak, on the other hand, the goal is to remove the gas as quickly as possible via the ventilation. This means that you have to decide what should be prioritized in view of the control of the ventilation should both incidents occur at the same time: the fire or the NH3 accident. The measures must be recorded in writing. In practice, the fire is usually treated as the first priority. Especially in this special area of application, it is not always so easy to make a blanket statement in advance about what is right or wrong now. However, if certain principles are observed, one is on the right track.
New SES guideline on gas detection systems
The new SES guideline "Gas detection systems" for the detection of gases and vapors is another documentwhich can assist you in the planning and installation of a gas detection system. The new guideline will be published in January 2022 and has been adapted according to the current technical innovations. Furthermore, the former two guidelines "Explosive Gases" and "Toxic Gases and Oxygen" have been combined in one document.
You will find in the guideline explanations of terms, the requirements for a GWA, for the gas detector, as well as the operation of various measurement principles of gas sensors and corresponding suggestions to which you must pay attention.
In the past, including recently, there have been repeated incidents in which, in addition to immense property damage, people have unfortunately been injured or killed. The following is a chronicle of what has happened recently:
There are incidents like this all the time, and they are by no means all incidents: I don't want to go so far as to say that all of these events could have been prevented with a GWA, but a gas warning system could definitely have had a positive impact on certain events and perhaps prevented worse. Nevertheless, one must realistically admit that not everything can be prevented with a GWA. Because there is still one essential point that must not be forgotten, and that is the human risk factor. We humans make mistakes. That is human and should be. You can learn from mistakes. Since this is a fact, it must be taken into account by repeatedly making people aware of the dangers and training them accordingly on how to properly handle GWA in their operations.
Some points to look out for are:
- What do I have to pay attention to?
- What does this flashing light or alarm horn mean?
- Where is the assembly point?
- However, this hazard analysis does not only refer to an industrial plant, but also to residential buildings that are equipped with gas warning systems. The people who live there must be trained and informed about how to behave in the event of a gas alarm, because untrained people often behave incorrectly and not infrequently make the situation even worse - for example, by activating a light switch in a cellar that contains an explosive gas mixture, which can cause it to ignite.
I think we all want to prevent that.