Always accessible, for back office and field staff
Product-related services are becoming increasingly important for the competitive position of manufacturing companies. Systematic service management is therefore of great importance. It serves as an instrument for innovative capability and market success.
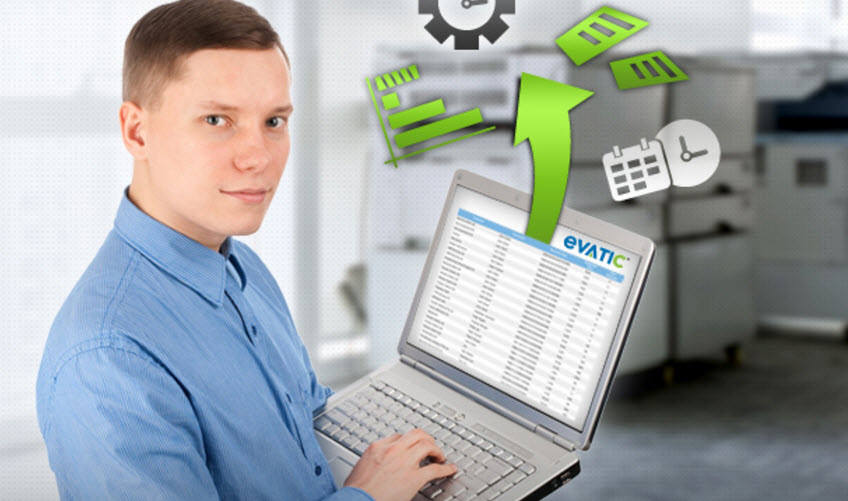
"We were still entering the individual orders on paper and also filling out the service reports manually. Furthermore, we lost a lot of time due to uncoordinated work routes, so that the technicians could only complete a few customer visits per day." Kay Ackermann, Head of TES - Technical Equipment & Service at Rivella AG
This was also recognized by the Beverage manufacturer Rivella from Rothrist, which until recently controlled its service and repair orders for its approximately 3,000 vending machines, refrigerators and fruit juice dispensers distributed throughout Switzerland with a "home-made" module of an enterprise resource planning (ERP) system. The problems mounted: "First, the processes were generally inefficient and complicated. Second, we only had two people who knew how to control the system," says Kay Ackermann, Head of TES - Technical Equipment & Service at Rivella AG. "We still entered the individual orders on paper and also filled out the service reports manually. Furthermore, we lost a lot of time due to uncoordinated work routes, so the technicians could only make a few customer visits per day."
User-friendly and pragmatic solution
Various factors played a role in the evaluation of the appropriate service management system. For example, the new tool had to be tailored to Rivella's specific maintenance tasks, have a modular design, be easy to use, and be cost-effective. Based on the overall package, Rivella subsequently decided on the Service Management System Evatic of Mathys Informatik AG in Unterentfelden. Managing Director Beat Mathys: "With Evatic, we are able to completely cover Rivella's specific requirements."
- This primarily includes the paperless, electronic work of the technicians using tablets, which replaces paper reporting. All the relevant information is stored on the tablets, such as machine type, service history, customer coordinates, and the configuration of the technical sales equipment. "The technicians only have to enter their service tasks once - and the information is already stored in the system for everyone to see," explains Beat Mathys.
- Evatic also automatically optimizes planning, for example, for maintenance tasks and quality control of technical sales equipment.
- At the same time, the system can be used to coordinate travel routes and thus save working hours.
- For the technicians, the automatic maintenance of the device history is a plus. This means that they always know what has happened to the individual machines in the past.
- The modular structure allows various extensions. At Rivella, we use three of them: "Evatic Service" as the central module for administration and scheduling," explains Beat Mathys. "Then 'Evatic Mobile Service', which acts as an interface module to the 'Evatic Service App' on the technicians' tablets. And 'Evatic Report Designer' for customizing reports and receipts."
- There is an automatic data transfer from Evatic to the ERP system used by Rivella and vice versa.
Interface as an easy hurdle
The project process went smoothly right from the start: The two companies drew up specifications and requirements, held a workshop with the specialist departments to explain the process flows, and set up an environment in which they tested all the processes one-to-one. Nevertheless, the project partners had to overcome a few minor challenges: All the people involved had to have the same level of knowledge of the work at all times, and an interface to the ERP system had to be established. The integrated interface is necessary to connect the two systems and thus ensure the constant exchange of data. "Due to the standardized and open data model, we were able to implement the interface with Evatic relatively easily within a few days and roll it out with the support of Rivella's internal ERP specialists," explains Beat Mathys.
"We are currently moving optimally in our field of activity, managing our employees in the back office and on the front line in a targeted manner and thus providing the best possible service for our customers." Kay Ackermann.
Look into the future
Rivella is glad that the administrative effort has been reduced considerably thanks to Evatic. "With Evatic, we are now much more flexible and dynamic on the road," says Kay Ackermann. "We can perform point-by-point evaluations and track exactly what has been incurred per device and customer within the scope of the contract and the service level agreement. This enables us to intervene quickly and replace a device if necessary."
No expansion with further modules is under discussion in the near future. "We are currently moving optimally in our field of activity, managing our employees in the back office and on the front line in a targeted manner and thus providing the best possible service for our customers," Kay Ackermann confirms.
Project facts
- Integration of the Evatic service management system at Rivella AG
- Server: Windows Server 2012/SQL Server 2012
- Internal scheduling workstations: Windows 7
- Mobile devices for technicians: Samsung Note 10 tablets
- Cost scope: under CHF 50,000
Mathys Informatics Ltd https://www.main.ch/