Strict guidelines easy to comply with
Quality management plays a special role in the automotive industry, as all major car manufacturers have imposed extremely strict guidelines on themselves that must be precisely adhered to. The requirements of the standards and customer specifications are extensive. A reliable and user-friendly software-based quality management system can help to ensure compliance with the standards.
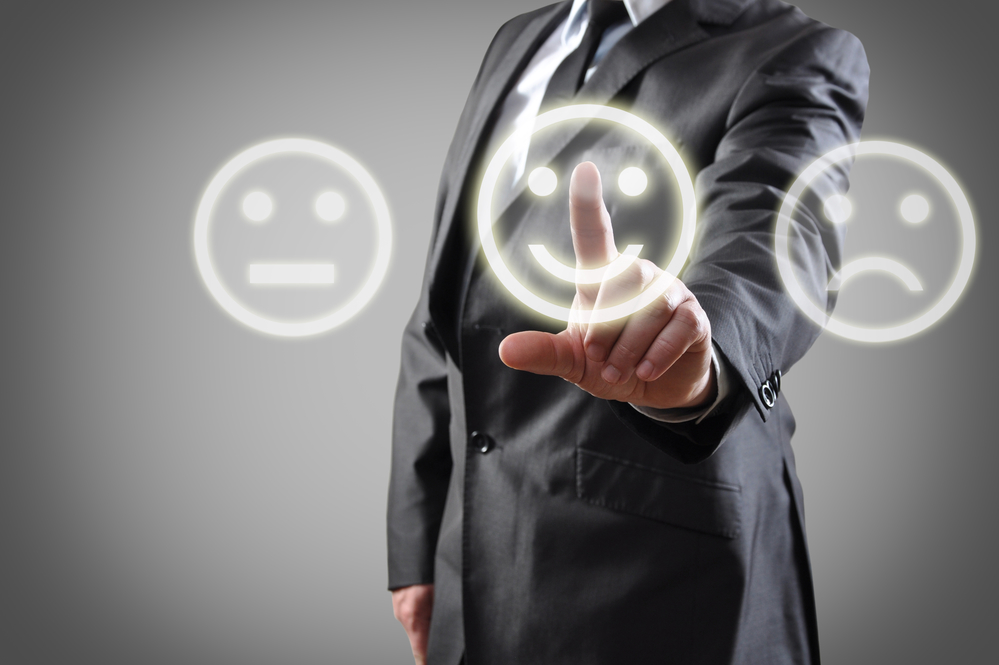
Oriented to the requirements of the DIN EN ISO 9001 series of standards, ISO/TS 16949 is additionally extended by some points that are of importance exclusively for the supplier industry. In addition to the benefits for all parties involved for more safety in the workplace, assured production conditions and capable processes, suppliers and manufacturers benefit from a solid cooperation oriented towards 0 defects. The customer can thus be guaranteed a qualitatively flawless product. Only those who comply with the rules create trust, can win over new business partners and survive on the market.
Software helps streamline and improve
The best technical tool is of little use if it is not user-friendly. Simplicity is needed here to avoid losing sight of the complicated jungle of standards and applications. The system administrator must be able to fulfill several normative customer requirements with an automated system and involve process owners. This means that the software can be used to improve products and processes as well as to streamline workflows.
There are many areas where compliance with legal requirements is mandatory, including the automotive industry, for example, with the road traffic requirements of the Federal Motor Transport Authority (KBA). This industry has the toughest regulations on the market with ISO/TS 16949, which requires some critical deliverables such as "measuring process performance ", "plant structure plans", "managing and avoiding recalls", the "special protection of employees" and a "contingency plan" that must guarantee delivery capability even in the event of incidents such as power failure, material problems or a sudden outbreak of influenza.
Simple modules for quality management
Compliance with the strict guidelines is only possible in a cost-efficient manner if tools are in use that support the user in avoiding errors. In this respect, many automotive manufacturers and suppliers rely on complex solutions, others on the use of various tools. At first glance, all-round tools represent the most convenient solution. However, many functions often remain unused or overwhelm the user.
Manufacturers such as MS QDS® AG offer 36 singular modules in their product portfolio that generate additional benefits when combined in a software system. Customers use the modules according to their individual requirements. At the same time, operation at the office level simplifies the application. MS QDS® AG focuses on the usefulness of such tools and not on useless "nice to have" functions.
In addition to clarity, the MS QDS® software system, for example, offers the following advantages: All entries for processes, departments and standards only need to be maintained in one place and are available for all other modules. Information about changes is automatically sent by e-mail and data from modules can be used in others.
Replacement for "slip box system
In the event of a defective product or a production process in need of optimization, it is crucial that modified documents can be made available in real time. Document control solutions that replace the "slip box system" by automatically storing all documents in a database are therefore particularly common.
However, not only process documentation, but also production itself can be made easier with suitable QM solutions. Production control plan tools and software for controlling and monitoring key figures provide an overview of all performance processes. Among other things, they can display the individual production stages and inform the user when tolerance values are exceeded.
Even the processing of complaints and support requests can be handled quickly and to the satisfaction of the consumer, supported by appropriate QM software, and constantly optimized. If the software does not deviate one millimeter from normative requirements, the best data for the next audit is obtained.
One solution - many advantages
After installation, employees immediately benefit from the sophisticated functions of user-friendly and practice-oriented solutions: Clear orientation within the clearly designed modules creates more security and reduces bureaucracy to a minimum. Since necessary activities are distributed to all process owners, QM awareness is better accepted by all hierarchical levels. Resources for process improvements are not only released at the system owner. The management level saves time by having a clear information structure that allows full and cost-efficient control over all processes.
Integrated measures management and the risk assessment required by the new ISO 9001:2015 are among the highlights, as are FMEA planning and project management for new development projects, taking APQP into account.
Efficient modules provide a reliable solution in quality management. In the end, what counts is the desired certification, compliance with strict standards, and fulfillment of customer-specific requirements.