Hazardous substances in 3D printing
The 3D printing market doubles approximately every three years. However, it is essential that companies using 3D printers address hazardous materials, radiation and explosion risks.
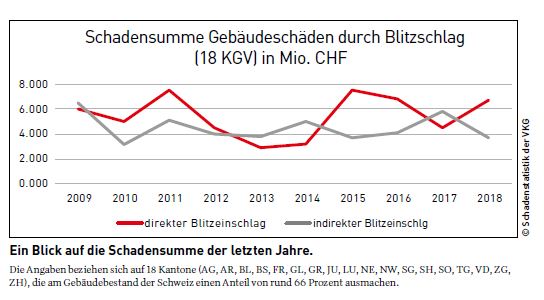
Whether 3D printing has ushered in a new age of production - as predicted - remains to be seen. The big hype seems to be over, but the fact is that additive manufacturing has arrived in many industries and is beginning to change the working world. The advantages for designers and developers are undisputed. High-precision and geometrically complex structures with filigree details and even integrated functions such as conductor paths can be manufactured from a wide variety of materials.
Additive instead of subtractive
When discussing the risks of "additive manufacturing," it is important to keep in mind that 3D printing is not a single or strictly defined technology. Rather, the term encircles dozens of manufacturing processes, the most important of which fall into one of the following types:
- powder bed based, e.g. selective laser and electron beam melting
- nozzle-based, e.g. laser buildup welding with powder or wire
- Material extrusion, in which, for example, filaments or granules of plastic are heated
- Photopolymerization/stereolithography, in which light-sensitive substances are selectively solidified by exposure to light, e.g. in additive microfabrication
What all 3D printing processes have in common is that software cuts the object designed on the computer into layers and outputs it as a digital data model to the printer, which assembles the three-dimensional component layer by layer. Since the objects are created by application rather than - as in milling, drilling, routing, sawing, planing, etc. - by removal, this process is referred to as additive manufacturing, in contrast to the conventional (mostly subtractive) processes. Initially, the greatest opportunities were seen in the automotive, aerospace and medical technology sectors, but now more and more areas of application are being added. Dental crowns or hip implants, designer jewelry or spare parts that are no longer available, artificial coral reefs or pedestrian bridges, components for space rockets or for submarines, the spectrum of 3D-printed components is immense. At the same time, the build envelopes of printers are getting larger, printing speeds are increasing, and printing processes are becoming more versatile as new starting materials are used. As a result, 3D printing is no longer limited to models and prototypes, but is evolving toward small-scale production and beyond.
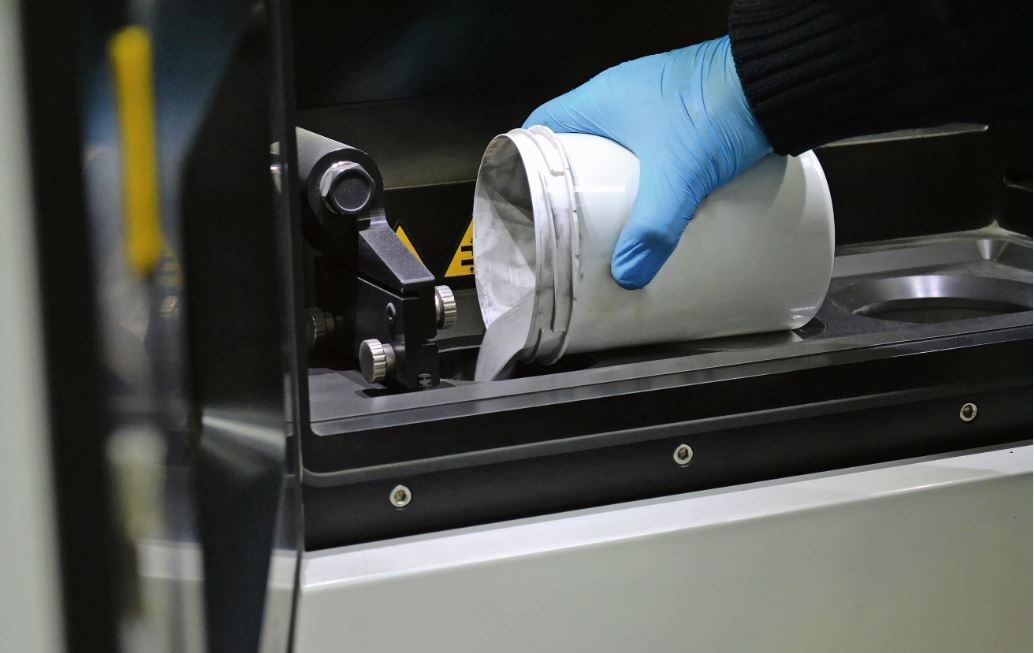
Hazards depending on material and printing process
At first glance, additive manufacturing production systems appear elegant and clean. Compared to classic processes, such as metalworking, a 3D printer is quiet, there is no oil dripping and no cooling lubricants splashing. But a deeper look at safety and health issues reveals material-specific as well as technology-specific hazards. 3D printers primarily use plastics, resins and metals. In addition, many other materials are printed, from ceramics and carbon fibers to concrete, marzipan and even living cells. The materials are usually in the form of powders or filaments, and more rarely as pastes, films or pellets. When it comes to "powder", every health protector will sit up and take notice; moreover, quite a few of the starting substances are considered hazardous materials. Other hazards are based on the printing technology. Depending on the process, there are radiation sources (laser, UV) or hot nozzles, and pollutants are also emitted. Thus, there is no one hazard in 3D printing, but one must look closely at each case, which materials are processed in which printer type and in which way.
Apply proven protection measures to 3D printing
The good news is that the health risks relevant to additive manufacturing are not completely new and proven protective measures are available. In many cases, these have already been implemented by the printer manufacturer. For many 3D printer models, enclosure is now standard, as is the fact that the printing process takes place in an inert atmosphere, i.e. under inert gas. For powder handling, there are the glove boxes known from laboratories, which allow working without powder contact, and other technical solutions. Nevertheless, any company planning to purchase a 3D printer would be well advised to consider the necessary safety precautions for the protection of employees at an early stage and in advance, e.g.:
- Which installation conditions of the printer have to be observed, which requirements apply e.g. for temperature, humidity, air exchange rate etc.?
- Can the printer be located in a separate room or separate from workstations that are in constant use?
- Is the floor in the designated printer room easy to clean?
- Do we need access control to the 3D printer workstation?
- Which solid, liquid and gaseous hazardous substances will be used, which will be created and will we protect people and the environment?
- Is shielding from the laser or UV radiation used guaranteed?
- How can we carry out all process steps, including cleaning, maintenance, filter changes, etc., without risk?
- Which steps in powder handling, such as filling, preparation, sieving, mixing, recycling of residual powder, etc., can or must we inertize?
- What protective equipment do employees handling powder need, such as gloves, eye protection, filter masks, possibly also disposable protective suits and blower-assisted respirators?
- How do we prevent the carry-over of powders into other work areas, e.g. by floor mats, changing rooms, self-closing intermediate doors, etc.?
- Do we need Ex-proof industrial vacuum cleaners with wet separators?
- Do we need special fire extinguishers for metal fires?
- If there is a risk of liquid splashes, can an eye shower be installed in the work area?
- Where and how do we want to store powder, where could an F90 safety cabinet be located, for example?
- Have we clarified how cleaning agents contaminated with powder, filter condensates, liquids from wet separators, etc. are disposed of properly?
In addition to the individual assessment of the situation on site - regardless of the printing process - are important sources of information for each user:
- the operating instructions with information on residual risks and protective measures
- name the safety data sheets of the starting materials, the risks and protective measures
The fact that 3D printers - at least for some printing processes - can now be found not only in DIY stores, but even on the rummage tables of discounters, should not tempt one to be lax when it comes to health protection. The following applies to such simple tabletop 3D printers, which are also used by private individuals or in schools: When used as intended and at the temperatures recommended for the respective filaments, the same recommendations apply in principle as for conventional printers indoors. It is important to ventilate regularly and that the exhaust air streams are not directed at the workplace. The hazards associated with 3D printing, such as fine dusts, volatile hazardous substances, gases or hot surfaces, are well known in occupational safety. Therefore, neither technical measures such as ventilation or exhaust systems nor suitable PPE nor rules for handling hazardous substances need to be newly developed. The crucial thing is to identify the risks on site and apply the measures that have been proven elsewhere. This is particularly true for companies that come from the traditional metal processing sector and have previously been exposed to hazards quite different from those posed by fine dusts or VOCs. Here, educating and training employees are crucial elements of successful prevention.
This technical article appeared in the printed edition SAFETY-PLUS 2-2022. Want to read the full article in this issue? Then close right away here a subscription.