Work errors are human caused
Prevention in occupational safety also helps to ensure that fewer work errors occur. The occupational safety specialists know the connection. The wider management is probably not yet as aware of it.
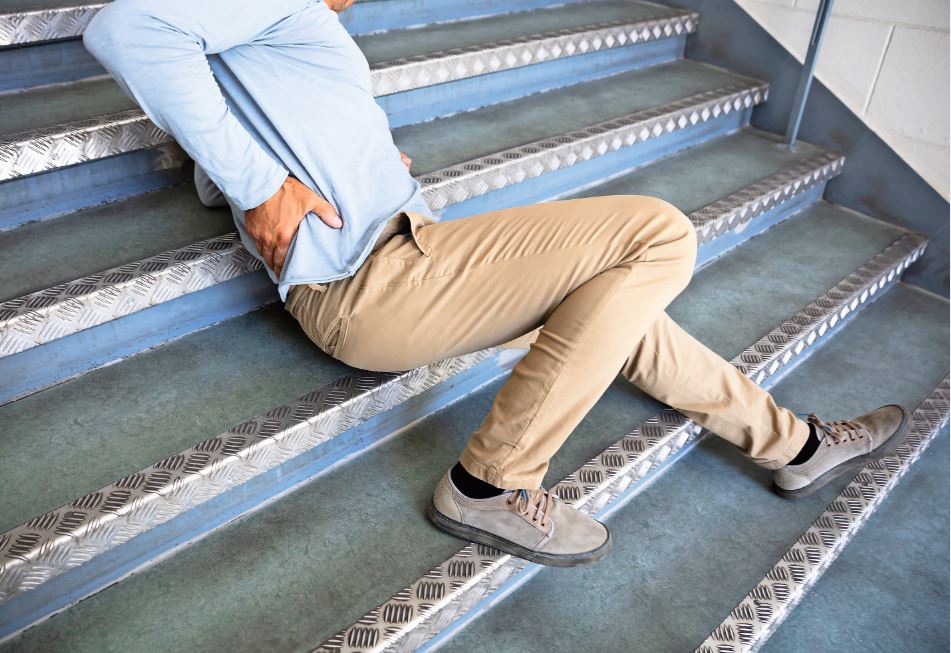
Deficiencies in occupational safety burden the effectiveness of work processes in several respects. If we feel threatened by a hazard, we constantly check whether we are still adequately protected. Such diffuse fear distracts us from the actual task at hand. It may even cause hectic activity. Because we want to get out of this unpleasant feeling as quickly as possible, we speed up the execution of the work task. We are less attentive and simply omit certain necessary operations and checks.
Work errors are human
If work errors occur more frequently or if it is a serious individual error, we look for the causes. We then distinguish between systematic and human-induced deviations from the target. Systematic errors occur when they are due to non-compliance with standards or because work equipment was defective, incorrectly or inaccurately set. Systematically caused errors can be precisely limited and permanently eliminated. If, however, it turns out that all work equipment is functioning perfectly and that the organization and specifications are consistent, the only remaining explanation is what is known as human error. If this is not the result of inadequate skills, everything seems to have been conclusively clarified.
If we are satisfied with this simple answer and have not tackled the root of the problem, these or similar mistakes will be repeated. The bad thing about this is that human errors do not occur systematically, but rather occur differently in time and place. Regardless of the distinction made, systematic errors are also humanly caused, only at a different stage of the work process based on the division of labor or starting from external influences.
Work errors are problematic under labor law
The German Federal Labor Court (BAG), for example, has clarified: "The employee must do what he is supposed to do and do it as well as he can." He owes the "work" and not the "work" (BAG 31.5.1992 - 2 AZR 551/91; BAG, 17.01.2008 - 2 AZR 536/06). Even an error rate that is three times higher than the department average does not justify termination (BAG, January 17, 2008 - 2 AZR 536/06). Above all, however, it must be excluded that the problem lies in the operational process, for example in suboptimal work processes, poor working conditions, work equipment or errors in personnel management (BAG, January 17, 2008 - 2 AZR 536/06).1).
Workers are therefore never a priori responsible for work errors. It is always the conditions under which work is performed that are decisive. Consequently, any zero defect strategy must focus on working conditions if it is to be successful.
In the publications of Suva as well as in the regulations and guidelines of the EKAS and VUV (Ordinance on Accident Prevention) we find concrete approaches for the identification of causes of errors and their elimination. They offer themselves as a basis for a checklist with, for example, the following points:
- Noise in the working environment
- Vibration in the working environment
- Workplace and environment lighting
- Explosion and fire hazard in the working environment
- Maintenance and waste disposal
- Mechanical hazards, for example from equipment
- Risk of tripping and falling, e.g. due to slippery floors and stairs, thresholds, obstacles on traffic routes
- Substances hazardous to health, e.g. due to gases, liquids, vapors from chemicals such as cleaning agents or solvents
- Strains on the musculoskeletal system, e.g. due to load transport, poor ergonomics
- Stresses caused by working environments, e.g. indoor climate, heat, humidity, etc.
- Physical stress, e.g. from noise, UV radiation
- Psychosocial stress, e.g. due to poor work organization, high work pressure, hectic pace, irregular working hours, etc.
Deficiencies based on this can trigger eye complaints, cause overtiredness and a drop in performance. Lack of concentration, fatigue, unpunctuality, forgetfulness, aggressiveness or even digestive disorders and high blood pressure are then early warning signs of a triggering of work errors.
Psychological aspects of work errors
Often, the blame for work errors is prematurely assigned to a specific person or group. This is not infrequently accompanied by threatening admonishments and serious accusations. We should not dismiss a worker with a high error rate without further ado. Instead, we should accept her as she is, if possible. We can hardly change individual human nature. Undoubtedly, an apparently incompetent person also has strengths. As soon as we succeed in recognizing them, we may even be able to adapt the demands made to the potential of the person in question. This then results in a win-win success that helps to avoid a possible threatening labor dispute.
Attention, a rigid prevention strategy against work mistakes is not harmless. It can cause excessive ambition or even lead to strict prohibitions. Affected persons then want to avoid even the most minor work errors at all costs, like an accountant. Even more fatal is not being allowed to make a mistake under any circumstances, like a surgeon. Both motivations can trigger severe psychosomatic stress disorders. If they are not treated psychotherapeutically, various health damages are to be feared. They can also be the cause of new human errors.
Conclusion
The technical organization of work processes, including the management of work errors on the one hand and the responsibilities for occupational safety on the other, are the responsibility of operationally autonomous units. Here, we would like to encourage consideration of how the two structures can be more closely interlinked.
This technical article appeared in the printed edition SAFETY-PLUS 1-2022. Want to read the full article in this issue? Then close right away here a subscription.